As an avid—albeit atypical, as a high school student—tour goer of the Minneapolis-St. Paul Parade of Homes in the early ‘90’s, a single universal feature remains in my mind: the steeply pitched, descending cascade of hipped roofs on nearly every home. I would marvel at the complexity of form on the exterior and all too often find disappointment in the flat, if tall, uniform ceilings tucked inside.
The trusses were not to blame. Roof trusses, formed of dimensional lumber segments and joined with pressed metal plates, were invented in the mid-20th century and revolutionized the residential wood-frame building industry in the following decades. Manufactured trusses are the original pre-fab, delivering complex roof geometry at low costs and exceptional speed, but rarely, and unfortunately, with little more creativity than an occasionally vaulted ceiling.
Drawing from my desire to discover something magnificent under those Parade home roofs, I have for years been exploring opportunities to create memorable and impactful interior space with economical pre-fabricated trusses.
In the early days of the pandemic, I began a new project on Lake Minnewaska, a glacial lake in West Central Minnesota, and recognized an opportunity. The relatively flat lakeside lot had good solar orientation but close neighbors to either side. The footprint of the original home was also surrounded by mature trees. Designing for single-level living and an open plan, both desires of the homeowners, meant finding opportunity for visual and spatial interest in the ceiling plane.
Through sketches and models, our team looked at ways to shape the ceiling to bring in light from above and define the space within. The notion of crisscrossing light monitors was appealing from the beginning, capturing the widest spectrum of daylight from sunrise to sunset, filtered through the canopy of trees. Here was an opportunity to surprise and delight with trusses!
We engaged Structural Design Concepts early in our process to ensure our ideas were sound and goals achievable—such as a ten-foot cantilever for covered outdoor dining. We provided SDC with Design Development drawings indicating our intentions, and in turn, they provided us with a truss layout for review.
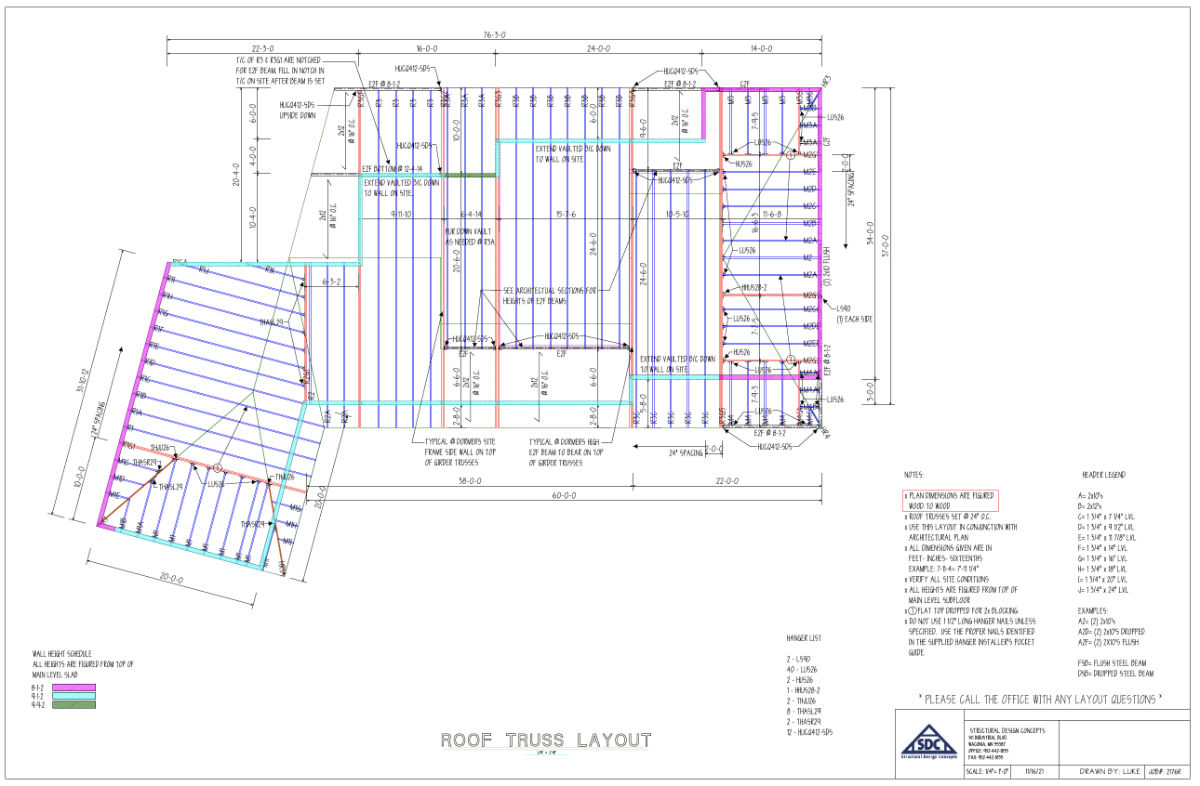
Truss designers and suppliers calculate individual truss members and connections for required loads and spans. There is typically some back and forth, confirming intent and clarifying bearing points, pockets and other details, before reviewing the final truss design package, truss by truss, and issuing approval. The trusses are then manufactured and delivered to the job site.
This project included roughly sixty individual truss profiles, all assembled using automation from a standard kit of parts, and identified on a layout provided by the manufacturer for efficient installation. The only unique characteristic of this truss package was the intention of design.
The end result surpassed all expectations. We were all smiles on the day of our photoshoot, a warm and beautiful fall day, in which the sun lit up the sky, and the highly anticipated project we were celebrating.